Silicone rubber heaters from Sinomas make it possible to achieve ennergy efficient and extremely flexible heating solutions. They take advantage of the unique properties of silicone rubber (low thermal mass, superb electrical insulation) to provide heating elements of unparalleled performance. Silicone rubber is calendared onto fiberglass cloth in a variety of thicknesses and constructions which serve as the basic insulation material for the heater. Fiberglass gives the heater dimensional stability without sacrificing flexibility.
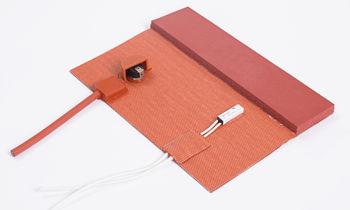
- Lightweight, thin, flexible
- Designed to the exact shape (including cutout) and size which conforms to the profile of customer devices.
- Etched foil resistive element, uniform heating
- -50°C to 220°C operating Temperature
- Moisture and chemical proof, optionally IP67
- Multiple installation method available
- Built-in temperature controller / sensor
- Thermal insulation or thermal conductive overlayer
- UL approved
Foil Element
Silicone rubber heater is available with etched foil elements or wire wound elements. Wire wound elements are wired manually according to pre-defined meander via the guide pins on the pattern board. Unless for irregular shaped 3D profiles or long heating tapes, wire wound technology has been phased out at SINOMAS.
The etched foil silicone rubber heater has exceptional heat transfer compared to wire wound heaters due to its large flat conductor surface. It can deliver more even heat profiles with higher watt density, providing longer service life. Beside chemical etching, for quick prototyping or large sized heating blanket, we can also produce the foil element by laser cutting.
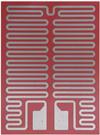
Factory Vulcanization / Preforming
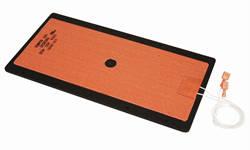
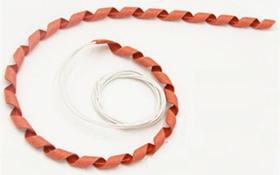
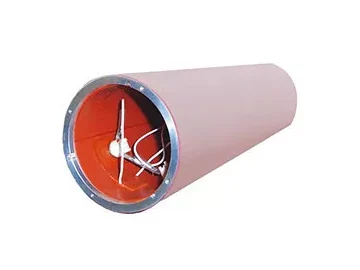
Through controlled process of heat and pressure, silicone rubber heaters can be factory vulcanized onto plain or black anodized Aluminum, stainless steel or other metal profiles / panels. The silicone rubber actually flows into the microstructure of the metal profile forming a permanent bond and allowing the most efficient heat transfer.
Factory vulcanization allows silicone rubber heaters to be designed at higher watt density and increases heater life. While the max watt density for standard silicone heater is 0.8 watts per cm2, factory vulcanization to Alunimum can support up to 3.0 watts per cm2 if the operation temperature is controlled.
Factory vulcanized heated metal profile has suprior performance than any field installation. With in-house metal workshop and extensive supplier network, we are able to supply high quality heating solution for any type of metal profiles.
By similar process but without a heat sink, silicone rubber heaters can be factory vulcanized / pre-formed into a shape (mostly cylindrical or spiral) permanently. The preforming greatly facilitates the installation of silicone rubber heaters on pipes and cylinders of small diameter or inside heater fitting of metal drums.
Waterproof Capability
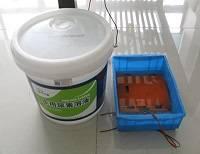
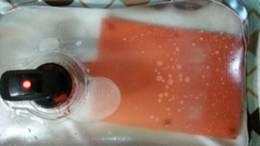
Silicone rubber heaters are generally moistureproof. Additional edge sealing will be enough for casual water spray. If the heater pad will operate under water for the long run, the whole heater has to be press molded to avoid any exposure of fiberglass to water. In this case, the thickness of heater pad will increase to about 2.6mm. Integrated temperature sensors are also possible.
The waterproof silicone pad heaters are very useful for humid environment or even fluid heating where conventional immersion heaters can’t be installed due to space or mounting limit. For example we have delivered silicone heating elements (2W/cm2) for portable hot water kettle, and heating blankets to maintain the temperature in the greenhouse.
Our teflon heaters and polyimide heaters can be used for immersion heating of fluids as well. Please consult us for chemical compatibility if you have such demand.
Temperature Rise Curve
The graph in the right illustrates the surface temperature rise of a standard silicone rubber heater with different watt densities. In the test the samples are hanged freely in an enclosed space.
The graph is supposed to give you an idea how fast the heating can be. It can’t take the place of engineering calculation and test for your specific applicaiton. The temperature in the real situation will be related to many different factors.
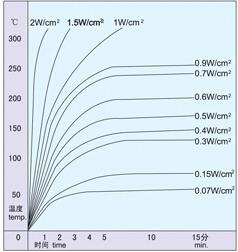